centrifugal casting|centrifugal casting machine for sale : manufacture Typical materials that can be centrifugal cast are metals, cements, concretes, glass, and pottery materials. Typical metals cast are See more Autoclave membrana 50 litri - zincato orizzontale [ped] I Vasi a Membrana Intercambiabile Z PED OR vengono utilizzati negli impianti di sollevamento dell’acqua ed hanno la funzione di .
{plog:ftitle_list}
Cryogens Safety Training This course provides an overview for the safe use and storage of cryogenic materials. The topics covered include physical properties of cryogens, hazards of working with cryogens, safe handling practices, and proper PPE. Any . See more
centrifugal castings company
Centrifugal casting or rotocasting is a casting technique that is typically used to cast thin-walled cylinders. It is typically used to cast materials such as metals, glass, and concrete. A high quality is attainable by control of metallurgy and crystal structure. Unlike most other casting techniques, centrifugal . See moreTypical materials that can be centrifugal cast are metals, cements, concretes, glass, and pottery materials. Typical metals cast are See more
Typical parts made by this process are pipes, flywheels, cylinder liners, and other parts that are axi-symmetric. It is notably used to cast See more
is the permit test hard in georgia
• Engineering portal• Rotating furnace – Device for making axially symmetric paraboloids• Spin casting – Method of utilizing centrifugal force to produce castings from a rubber mold• See more• animation of centrifugal casting process• Efunda site page with centrifugal casting fundamentals• Centrifugal Casting Video• Cylinder Liner Manufacturing (Centrifugal Casting Process Video) See moreIn centrifugal casting, a permanent mold is rotated continuously at high speeds (300 to 3000 rpm) as the molten metal is poured. The molten metal spreads along the inside mold wall, . See moreCylinders and shapes with rotational symmetry are most commonly cast by this technique. Long castings are often produced with the long axis parallel to the ground rather than standing up in order to distribute the effect of gravity evenly.Thin-walled . See more
• Kalpakjian, Serope; Schmid, Steven R. Manufacturing Engineering and Technology (5th ed.). p. 525. See more Advantages and Limitations of Centrifugal Casting: Centrifugal casting offers a blend of technical advantages and efficiency gains, balancing high-quality output with specific operational challenges that require expert management and meticulous process control. Advantages of Centrifugal Casting: Mitigation of Internal Defects:
Centrifugal casting is a more efficient casting process, however, since the dies can be used multiple times. Of course, there are no cores created with centrifugal casting, which is a good thing since it minimizes waste. With centrifugal casting, the liquid material is distributed onto the inner walls of the mold cavity. As a result, the newly .Horizontal centrifugal casting machines are used to cast ferrous and non-ferrous castings that are longer in length than they are wide in diameter. Equipped standard with water cooling and variable speed drives. Machine Types: Trunnion Type Machines; Dual Faceplate Machines;
Centrifugal casting is a versatile and efficient metal casting process used to create high-quality, thin-walled cylindrical parts. It uses centrifugal force generated by the rotation of a mold to distribute molten metal evenly throughout the cavity.Centrifugal casting has a wide range of applications in the industry and is used to make parts such as bushings, engine cylinder liners, rings, brake drums, water supply lines, sewage pipes, street lamp posts and gas pipes. Centrifugal casting offers several unique advantages. Hence centrifugal casting is done for producing various parts for .The centrifugal casting method is the method to produce pipes by pouring molten metal into a rapidly spinning cylindrical mold in which centrifugal force from the rotation exerts pressure on the molten metal. In 1952, Kubota developed its first centrifugal casting technology for steel. Since establishing a framework for industrial-scale mass . Centrifugal castings tend to provide greater value as part diameters and wall sections increase. Good Foundry Practices Required. Although many claims are made concerning the superior properties obtainable from centrifugal castings, the process alone is not a guarantee of a superior product. In cases where equipment and design permit the full .
Exploring Casting Processes: Continuous vs. Centrifugal Casting for Bronze Bushings The decision between continuous casting and centrifugal casting for bronze bushings hinges on factors such as desired product properties, design complexity, and application requirements. Each method has unique advantages for shaping molten metal into essential . Centrifugal casting is a highly efficient and versatile metal casting process that harnesses centrifugal force to create high-quality, cylindrical-shaped components with exceptional strength and integrity. By spinning a mould at high speeds, molten metal is forced against the inner surface, resulting in a controlled solidification process that ensures uniformity and .
Mailing Address: Centrifugal Castings, Inc. P.O. Box 210 Temple, Texas 76503. Physical Address: Centrifugal Castings, Inc. 3320 Parkway Dr. Temple, Texas 76504
Centrifugal casting is a unique manufacturing technique that has revolutionized the way many industries produce components. This technology was discovered in the early 1800s and has emerged as the most reliable and cost-effective method of creating high-quality parts in many applications.
Vertical centrifugal casting machinery spins parts about a vertical axis. Parts are commonly of shorter height than diameter. The great benefit of spinning about a vertical axis is that practically any size and shape of casting can be spun about a vertical axis. Common castings poured in vertical machinery are rings and ball valve balls. Dr. Dmitri Kopeliovich Centrifugal casting is a method of casting parts having axial symmetry. The method involves pouring molten metal into a cylindrical mold spinning about its axis of symmetry. The mold is kept rotating till the metal has solidified.. As the mold material steels, Cast irons, Graphite or sand may be used.. The rotation speed of centrifugal mold is .Learn more about Centrifugal Casting and Delta Centrifugal: https://www.deltacentrifugal.com/Centrifugal casting is a method used to produce metal products t.Experience precision in metal with our centrifugal casting process at our advanced centrifugal casting foundry. For top-notch parts and service, contact us now! Office: 888-433-3100 US & Canada +1-254-773-9055 International. Fax: +1-254-770-1011. Mail: [email protected]. Get A Quote. Home; About Us.
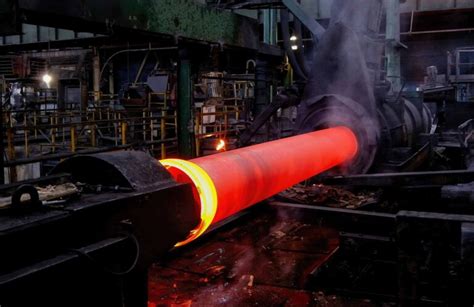
Founded in 1982, we have earned a reputation as a top centrifugal foundry with a commitment to quality and meeting the specific needs of our customers. We provide castings from 3” to 35 1/2” O.D., and a full range of on-site services including cutting, heat treating, chemical analysis, rough and finish machining. Centrifugal casting stands out as a remarkable process in the realm of metal fabrication, offering unparalleled quality and versatility. Its ability to produce components with enhanced mechanical properties and purity makes it a preferred choice in various industries. For those in need of such high-grade components, partnerships like Millstream .During WWII, Nat was the centrifugal casting expert on the U.S. War Metallurgy Committee." Nat held several U.S. patents and was the designer of numerous horizontal, vertical and face-plate machines, as well as high production special purpose machines. He is the author of the book Centrifugal Casting, which is still considered to be the .
Centrifugal casting is a casting technique that involves pouring molten metal into a rapidly spinning cylindrical mold, also known as 'liquid forging'. The mold continues to rotate until the completion of solidification of the poured melt, resulting in a thin-walled cylinder. This method improves the density of the metal, increases the actual . The document discusses centrifugal casting, which involves pouring molten metal into a rotating mold. As the mold rotates at around 1000 rpm, centrifugal force throws the liquid metal against the mold walls where it solidifies into the final shape of the casting. Common mold materials include steel, cast iron, and graphite.
Centrifugal casting employs a unique mechanism where high centrifugal force isolates less dense substances, pushing them to the casting’s bore area. This phenomenon, often called “secondary refining,” ensures that impurities like metal oxides, sulfides, and gas are separated, leaving behind a pristine, defect-free part. In this video we have explained everything about centrifugal casting with simple animation. Centrifugal casting works by centrifugal force. Physics behind ce.
Centrifugal casting, also known as spin casting or centrifugal die casting, is a metal casting process used to create hollow cylindrical components. In this method, molten metal is poured into a rotating mould, which can accommodate profiles up to 236”/6000 mm in diameter. The centrifugal force generated by the spinning mould forces the metal . Centrifugal casting is an option for producing complex geometries with less waste and better energy efficiency. This is accomplished by controlling the ramp-up acceleration of the turntable where rotational velocity is a time-dependent function of rotational radius and molten metal mass, taking into account the flow rate and cooling rate of the liquid.
Centrifugal casting is therefore utilised as a candidate production method, as under the centrifugal force, metal can rapidly fill thicknesses substantially less than a millimetre before it .
Centrifugal casting is a manufacturing process used to produce cylindrical components by using the forces generated by centrifugal motion. Centrifugal casting is a highly efficient and versatile process for producing high-quality cylindrical and symmetrical parts. Its ability to produce parts with superior mechanical properties and minimal .Not all alloys can be cast using the centrifugal casting method: Industries and products. Some numerous industries and applications benefit from the centrifugal casting method. The process reliably yields a tubular shape with consistent strength and high material purity from roll .
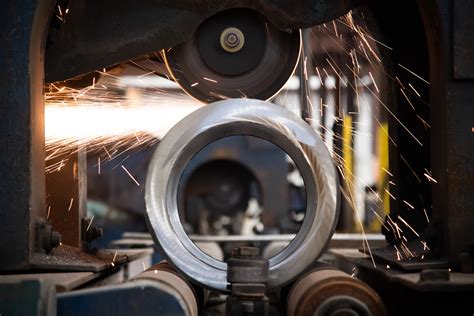
is the permit test hard in texas
In this video, we will learn about autoclave types and their uses in the microbiology laboratories. the autoclave has three types. autoclave uses in hindi,a.
centrifugal casting|centrifugal casting machine for sale